I costi di manutenzione contribuiscono per gran parte del totale dei costi operativi di tutti gli impianti manifatturieri o di produzione. Tali costi variano mediamente, in funzione della tipologia di industry, tra il 15 ed il 60 percento del costo del prodotto finito.
Uno dei tasselli più importanti per ottenere una riduzione sostanziale dei costi di manutenzione ed incrementare la disponibilità dei propri macchinari produttivi è sicuramente lo sviluppo e l’implementazione di modelli predittivi di guasto dei componenti critici di impianto robusti ed affidabili.
Indice degli argomenti
Manutenzione predittiva, che cos’è
Tali modelli devono essere in grado di:
Guida all'AI nel manifatturiero per il 2025: inietta nuova energia nella tua attività
- Segnalare anomalie di funzionamento fin dall’insorgere dei primi segnali di fenomeni di degrado (anomaly detection);
- Effettuare diagnosi precoci del modo di guasto, classificando ogni anomalia connessa all’insorgenza di fenomeni di degrado con nel corretto modo di guasto (diagnostic model);
- Valutare la vita utile residua (RUL – Remaining Useful Life) del macchinario di interesse (RUL prediction).
Riuscire in questa difficile sfida, permetterebbe di:
- Ridurre al minimo il numero di interventi manutentivi non programmati grazie all’intercettazione precoce di ogni fenomeno di degrado (anomaly detection), alla corretta classificazione del relativo modo di guasto (diagnostic model) e alla stima della vita residua del macchinario in analisi (RUL prediction);
- Ottimizzare la programmazione degli interventi manutentivi di concerto con la programmazione della produzione, grazie alla stima della vita utile residua che permette di pianificare con largo anticipo tutti gli interventi manutentivi nei fermi macchina programmati;
- Ottimizzare il costo logistico delle parti di ricambio. La previsione di quando un determinato componente si guasterà (RUL prediction) permette di applicare la filosofia JIT (Just in Time) nell’approvvigionamento delle spare parts con evidente riduzione di tutti i costi legati alla gestione delle scorte a magazzino;
- Incrementare la disponibilità dei propri macchinari, sfruttando al massimo il tempo produttivo tra guasti. Conseguenza di una corretta pianificazione degli interventi manutentivi di concerto con le esigenze produttive.
Come funziona la manutenzione predittiva
In questo contesto, si inserisce a pieno il concetto di manutenzione predittiva, una delle tre principali tecniche manutentive insieme alla manutenzione a guasto e alla preventiva, è definita dal CEN (European Committee for Standardization) e della UNI 10147 come “la manutenzione basata sulle condizioni, effettuata a seguito di una previsione derivata da analisi ripetute o caratteristiche note e valutazione dei parametri significativi del degrado del componente”.
“…Comprende il rilevamento e la misurazione di uno o più parametri e l’estrapolazione, secondo i modelli appropriati, del tempo rimanente prima del guasto o RUL (Remaining Useful Life)”. Quest’ultima caratteristica è ciò che la differenzia dalla manutenzione su condizione basata sul concetto di asset monitoring ovvero della “sola” individuazione dell’insorgenza di anomalie di funzionamento.
Inoltre, la manutenzione predittiva, parte dalla premessa che un monitoraggio continuo delle attuali condizioni meccaniche, di efficienza ed altri indicatori delle condizioni operative del treno macchine e dei sistemi di processo, forniscano i dati necessari a garantire il massimo intervallo tra interventi manutentivi, minimizzando il numero ed il costo di interruzioni di produzione non schedulati.
Per ottenere un modello predittivo robusto ed affidabile è quindi necessaria l’applicazione di una vasta gamma di sensori ai macchinari e l’implementazione di una forte infrastruttura tecnologica ed informatica (ICT – Information and Communication Technology) che permetta il loro monitoraggio continuo e la loro analisi sia online che offline..
Stato dell’arte delle tecniche di manutenzione predittiva
Nonostante l’elevato costo di investimento in ICT (Information and Communication Technology) e sensoristica necessari allo sviluppo di un sistema di manutenzione predittiva, questa risulta la tecnica di manutenzione preventiva più appropriata nell’89% dei modi di guasto (Hashemian, 2010).
L’interesse degli studiosi, verso questa politica manutentiva è sempre maggiore anno dopo anno fin dal primo articolo pubblicato nel 1952, come mostrato dal grafico in Figura 1:
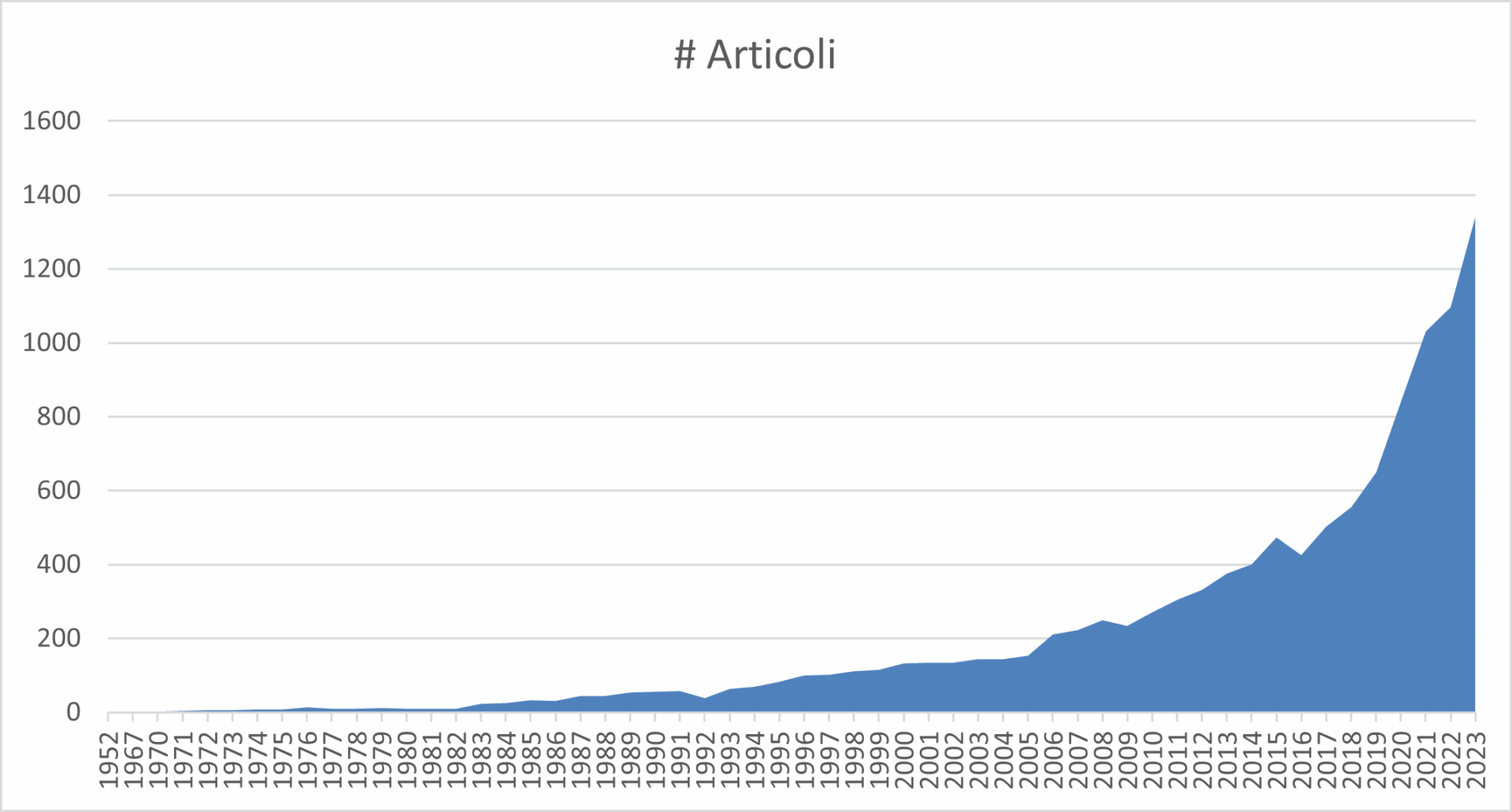
Figura 1 Numero di articoli pubblicati per anno (Keywords: Predictive Maintenance, Limits: Articles Fonte: Scopus.com)
Indice di quanto anche il mondo industriale abbia a cuore questa tematica. Delle migliaia di articoli scientifici presenti sui principali motori di ricerca, ne sono stati selezionati e studiati nel dettaglio 58 che rispecchiano i seguenti criteri di appropriatezza e rilevanza:
- Interpretazione del concetto di predictive maintenance in linea con la definizione data dalla UNI 10147 cioè che ;
- Articoli che permettessero di passare dalla teoria alla pratica: in cui si raccontano use-case reali con riferimento esplicito ai componenti/macchinari ed alle tecniche di stima della RUL utilizzate.
Tutto ciò allo scopo di fornire un quadro chiaro e aggiornato di:
- Paesi del mondo particolarmente sul pezzo nella ricerca applicata di questo topic;
- Settori industriali più interessati alla manutenzione predittiva;
- Componenti e macchinari per i quali la ricerca ha dato risultati concreti in termini di tecniche predittive
- Tecniche di stima della RUL maggiormente studiate ed utilizzate.
Analisi delle aree geografiche degli articoli
Per capire quale sia il Paese più interessato alla predictive maintenance, è stata fatta una ricerca utilizzando come metro di valutazione i finanziatori dei singoli articoli:
- Nordamerica: U.S. Department of Energy, US National Science Foundation;
- Sudamerica: CAPES, FAPEMIG, CNPq e FINEP in Brasile, Departement o Administrativ o de Ciencias in Colombia;
- Asia: National Natural Science Foundation of China, Singapore Ministry of Education through the Academic Research Funding, Toyota Motor Corporation, Ministry of Science and Technology Israel, Korea Electric Power Corporation, Korea Institute of Energy and Technology Evaluation and Planning;
- Oceania: Australian Government Endeavour Post-doctoral Fellowship award;
- Europa: Politecnico della Slesia, Swedish Agency for Innovation Systems, Franco-Swiss INTERREG IV, European Commision.
È stata quindi fatta una percentuale del rapporto tra il numero degli articoli che i singoli finanziatori hanno supportato e il numero totale di articoli analizzati. I risultati sono rappresentati In Figura 2:
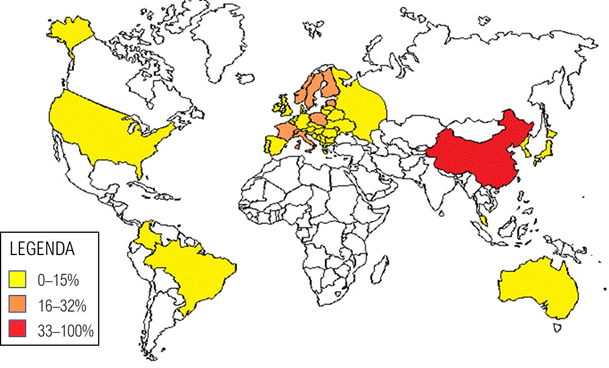
Figura 2 Paesi finanziatori degli articoli selezionati
Emerge chiaramente dalla figura come la National Natural Science Foundation of China sia il principale finanziatore a livello mondiale.
Analizziamo adesso i settori industriali.
Analisi dei settori industriali degli articoli selezionati
Successivamente sono stati analizzati i settori industriali maggiormente coinvolti nella ricerca sulla manutenzione predittiva e rappresentati in Figura 3:
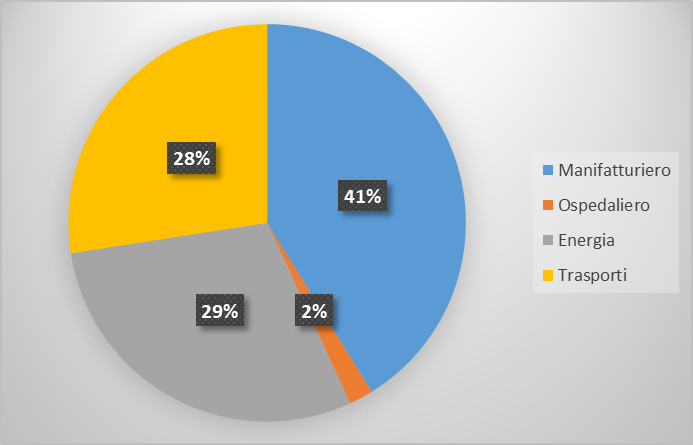
Figura 3: Settori industriali degli articoli selezionati
Come si può osservare, il settore manifatturiero è il più interessato con il 41% seguito dai trasporti e dal settore energetico.
Analisi dei componenti trattati negli articoli selezionati
Passiamo quindi all’analisi dei componenti studiati in questi articoli. Come si evince dalla Figura 4, i componenti studiati sono molti e molto differenti tra loro, sono sia componenti elettrici ed elettronici (lampadine LED, batterie ecc.) che meccanici, con una maggiore concentrazione verso quest’ultimi ed in particolare: cuscinetti (35%), turboventole (20%) e turbine (9%). I modelli di previsione della RUL sono in effetti più efficaci su componenti meccanici con parti in movimento, soggette quindi a fenomeni di degrado dovuti a fatica ed usura meccanica.
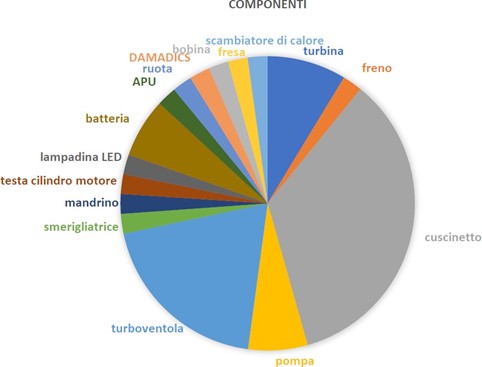
Figura 4 Componenti trattati negli articoli selezionati
Analisi delle tecniche di stima della RUL
Come abbiamo già spiegato in precedenza, il modello di previsione della RUL (o prognostic model) è centrale per la manutenzione predittiva ed è di fatto l’abilitatore della maggior parte dei benefici che si ottengono da questa tecnica manutentiva. Per questo ci siamo concentrati sull’analisi delle tecniche ed i modelli utilizzati proprio per la stima della vita utile residua dei componenti e macchinari negli articoli selezionati.
I modelli di previsione RUL possono essere classificati in:
- physical models:
I modelli basati sulla fisica comportano una descrizione matematica del processo di degrado del sistema per stimare la RUL. Nonostante l’output di tali modelli tenda ad avere un significato fisico diretto, è richiesta un’ampia quantità di dati empirici e, inoltre, i modelli sono costruiti caso per caso non permettendo l’applicabilità a sistemi diversi.
- data-driven models (Statistici o Machine learning):
I modelli basati sui dati sono composti da dati precedentemente osservati per prevedere il futuro stato del sistema e tra questi si trovano modelli statistici, funzioni di affidabilità e modelli di intelligenza artificiale. Trattandosi di dati storici tali modelli sono applicabili solo quando si ha a disposizione una sufficiente quantità di dati. L’output generato tende a fornire informazioni più precise rispetto a quelle ottenute dall’esperienza, tuttavia, la maggior parte dei risultati di tali modelli è difficile da correlare ad un significato fisico in special modo se utilizzano tecniche di machine learning black-box.
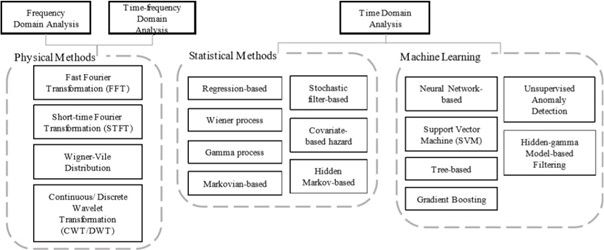
Figura 5 Classificazione modelli prognostici (Lee et al., 2019)
Analizzando il numero di articoli facenti parte dei metodi fisici, statistici e machine learning, emerge che il metodo statistico è il più utilizzato e riscontrato in 35 dei 58 casi (60%) contro i 23 (40%) in cui vengono impiegate tecniche appartenenti ai metodi machine learning. I modelli fisici, negli articoli selezionati, non vengono utilizzati per la previsione della RUL ma in fase di preelaborazione dati per estrarre le feature più informative dai dati storici.
Inoltre, emerge che le variabili spia che meglio descrivono i fenomeni di degrado sono: vibrazione, temperatura pressione, usura e velocità.
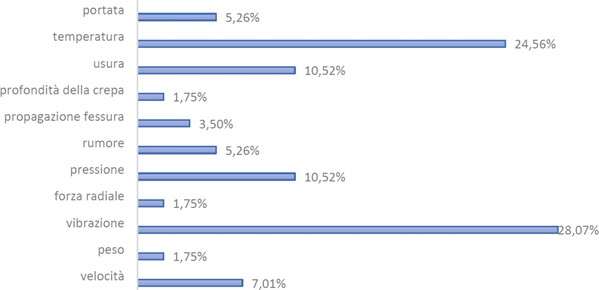
Figura 6 Variabili considerate per la stima della RUL
Manutenzione predittiva, cosa dicono i dati
Adesso che sappiamo quali sono i componenti analizzati, quali variabili sono state monitorate e che tipologia di modello è stato utilizzato, non resta che incrociare i dati per ottenere delle interessanti matrici di relazione.
Di seguito vengono riportate delle analisi incrociate componente-variabile e componente- metodo.
Tabella 1 Analisi componente analizzato – variabili selezionate
Usura | Portata | Temperatura | Propagazione fessura | Profondità crepa | rumore | pressione | Forza radiale | vibrazione | peso | velocità | |
Turbina | X | X | X | ||||||||
Freno | X | X | X | ||||||||
Cuscinetto | X | X | X | ||||||||
Pompa | X | X | |||||||||
Turboventola | X | X | X | ||||||||
Smerigliatrice | X | X | |||||||||
Mandrino | X | X | X | ||||||||
Testa cilindro motore | X | ||||||||||
Lampada LED | X | ||||||||||
Batteria | X | ||||||||||
motore | X | X | |||||||||
APU | X | X | |||||||||
Ruota | X | ||||||||||
DAMADICS | X | ||||||||||
Bobina | X | X | X | ||||||||
Fresa | X | ||||||||||
Scambiatore calore | X | X | X |
Tabella 2 Analisi componente analizzato – metodo scelto
Statistical methods | Machine Learning | |
Turbina | X | X |
Freno | X | |
Cuscinetto | X | X |
Pompa | X | X |
Turboventola | X | X |
Smerigliatrice | X | |
Mandrino | X | |
Testa cilindro motore | X | |
Lampada LED | X | |
Batteria | X | |
motore | X | |
APU | X | |
Ruota | X | |
DAMADICS | X | |
Bobina | X | |
Fresa | X | |
Scambiatore calore | X |
Conclusioni
In estrema sintesi, la manutenzione predittiva con un costo di investimento iniziale non trascurabile è in grado di:
- ridurre il costo di gestione della manutenzione e di conseguenza del prodotto finito;
- incrementare la disponibilità dei macchinari di impianto;
- ottimizzare la schedulazione degli interventi manutentivi riducendo i fermi macchina indesiderati;
- ottimizzare la gestione logistica delle spare parts abilitando la possibilità di gestione JIT.
La Cina risulta ad oggi il maggior finanziatore a livello mondiale della ricerca applicata nel campo della manutenzione predittiva, ma d’altro canto è anche uno dei Paesi in cui si ha una grande presenza di industrie manifatturiere che abbiamo visto essere il settore industriale che più si è avvicinato negli ultimi anni alla tematica.
Il componente maggiormente studiato è di gran lunga il cuscinetto e la vibrazione è la variabile spia più analizzata. Infine, le tecniche statistiche battono 3 a 2 le tecniche machine learning, anche se in effetti è molto difficile stabilire una linea di confine netta tra i due mondi che sono così simili in quanto appartenenti alle tecniche di data-driven analysis.
Una volta inquadrato il contesto generale della manutenzione predittiva, sarebbe interessante indagare il connubio tra le tecnologie 5.0 e la gestione della manutenzione oltre alla definizione di una roadmap per l’implementazione sul campo di un sistema di manutenzione predittiva.
Diventa competitivo nell'era dell'Industria 5.0: Ecco le tecnologie per una Manifattura Intelligente
Bibliografia
- Hashemian, H.M., 2010. State-of-the-art predictive maintenance techniques. IEEE Trans. Instrum. Meas. 60, 226–236.
- Lee, C.-Y., Huang, T.-S., Liu, M.-K., Lan, C.-Y., 2019. Data science for vibration heteroscedasticity and predictive maintenance of rotary bearings. Energies 12, 801
- Lee, J., Qiu, H., Ni, J., Djurdjanovic, D., 2004. Infotronics technologies and predictive tools for next-generation maintenance systems. IFAC Proc. Vol. 37, 291–302.
- Liao, L., Köttig, F., 2014. Review of hybrid prognostics approaches for remaining useful life prediction of engineered systems, and an application to battery life prediction. IEEE Trans. Reliab. 63, 191–207.
- Mobley, R.K., 2002. An introduction to predictive maintenance. Elsevier.