Le tecnologie promosse dal paradigma di Industria 5.0 possono rappresentare un supporto nella gestione della manutenzione predittiva. Analizziamo, con una visione più pratica che teorica, gli strumenti a supporto dell’implementazione di una gestione avanzata ed innovativa della manutenzione.
Passeremo quindi da una breve ma dovuta disamina delle innovazioni introdotte dalle cinque rivoluzioni industriali, dalla descrizione dettagliata delle tecnologie abilitanti il 5.0 e la loro declinazione a supporto della gestione della manutenzione, in un contesto produttivo sempre più caratterizzato dall’automazione industriale.
Indice degli argomenti
Industria 5.0 e le tecnologie per la manutenzione predittiva
Negli ultimi 15 anni, con lo sviluppo delle nuove tecnologie dell’informazione, è emerso il paradigma della quarta rivoluzione tecnologica, ovvero l’Industria 4.0. Questo concetto si basa su tecnologie eterogenee di integrazione di dati e conoscenze che includono i sistemi cyber-fisici (Cyber Physical Systems – CPS), l’Internet of things (IoT), l’Internet dei servizi e il cloud computing, mantenendo una continua interazione e scambio di informazioni. Il suo obiettivo finale è quello di raggiungere una maggiore efficienza operativa, produttività e automazione, migliorando l’efficacia e l’efficienza.
Considerando che un aspetto importante dell’Industria 4.0 è la capacità dei sistemi di produzione di monitorare i processi fisici, creando una copia digitale (“Digital twin”) del sistema fisico, rendendo così possibile la messa in atto di decisioni intelligenti ottenute grazie alla comunicazione in tempo reale e alla cooperazione con esseri umani, macchine e sensori è chiaro come l’Industria 4.0 sia un processo industriale di gestione del valore aggiunto e della conoscenza, supportato dall’uso di tecnologie informatiche e algoritmi avanzati.
Con il Decreto-Legge n. 19 del 2 marzo 2024 è stato istituito il Piano Transizione 5.0. Il Piano, in complementarità con il Piano Transizione 4.0, si inserisce nell’ambito della più ampia strategia finalizzata a sostenere il processo di trasformazione digitale ed energetica delle imprese. Se da un lato il piano Industria 4.0 sostiene la trasformazione digitale delle imprese incentivando gli investimenti privati in beni strumentali tecnologicamente avanzati, in attività di innovazione e riqualificazione delle competenze, dall’altro con il 5.0 si intende sostenere la transizione dei processi di produzione verso un modello efficiente sotto il profilo energetico, sostenibile e basato sulle energie rinnovabili.
È quindi evidente come il nuovo paradigma industriale non abbia introdotto nessuna innovazione sotto il profilo tecnologico ed infrastrutturale rispetto alla precedente risalente ad appena 13 anni fa, ma si differenzi sostanzialmente per l’obiettivo. Le tecnologie promosse da entrambi i piani sono quindi il mezzo necessario per arrivare all’obiettivo finale: da un lato la digitalizzazione delle imprese, dall’atro l’efficientamento energetico e la sostenibilità.
Precedenti rivoluzioni industriali
La prima rivoluzione industriale ha avuto origine nella seconda metà del XVIII secolo, segnata da numerose invenzioni nell’ambito delle macchine industriali. La più importante fu il motore a vapore di Thomas Newcomen. L’uso massiccio di macchine a vapore ha portato a un miglioramento della produttività e dei trasporti, contribuendo al miglioramento del benessere globale portando ad una rapida crescita della popolazione.
La seconda rivoluzione industriale è stata caratterizzata dall’introduzione della produzione di energia elettrica e risale all’inizio del XX secolo. È stata caratterizzata anche dall’introduzione del concetto di produzione di massa (ad esempio le linee di assemblaggio di Henry Ford). Un’importante innovazione fu l’introduzione del principio della divisione del lavoro: le persone non producevano più prodotti dallo stato iniziale a quello finale, ma si specializzavano in task specifici. L’apprendimento dei compiti ripetitivi è stato rapido e facile e ha aumentato il valore aggiunto.
La terza rivoluzione industriale è iniziata negli anni ’70 del XX secolo con lo sviluppo dell’elettronica e delle tecnologie dell’informazione e della comunicazione. Le innovazioni più importanti che hanno caratterizzato quest’epoca sono state i computer, le comunicazioni mobili e Internet.
L’introduzione dei sensori, degli attuatori e della tecnologia di automazione di controllo dei macchinari nella produzione ha trasformato il contesto industriale, consentendo la riduzione dei costi e portando ad un ulteriore aumento della produttività.
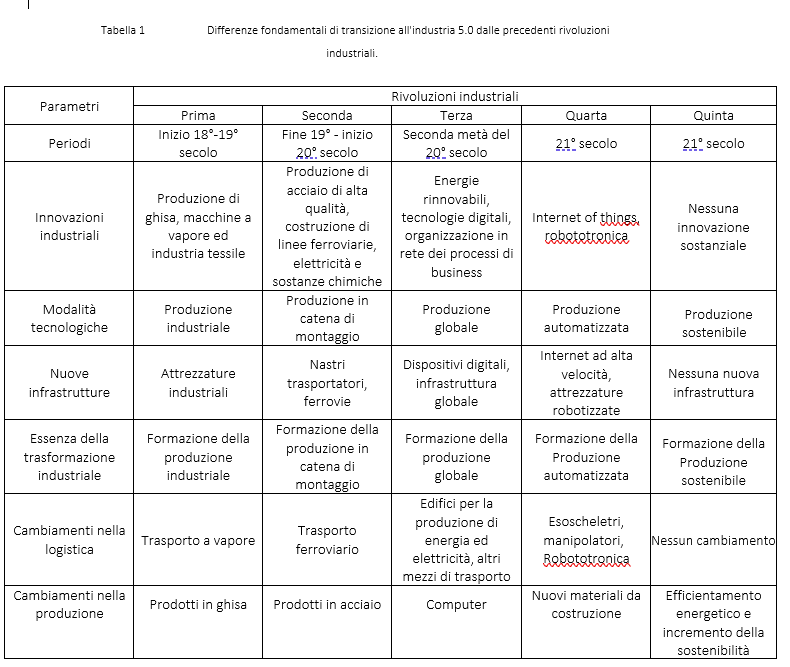
Tecnologie per la manutenzione predittiva, gli aspetti chiave
Per riassumere i principali aspetti dell’innovazione tecnologica descritti dal paradigma Industria 4.0 e ripresi nel successivo 5.0, nella letteratura scientifica sono state individuate nove tecnologie chiave, o “pilastri”:
- Internet of Things (IoT);
- Big Data e Analytics;
- Simulazione;
- Cloud;
- Sistemi integrati;
- Realtà aumentata;
- Robot autonomi;
- Produzione additiva;
- Sicurezza informatica.
Internet of things
L’IoT è stata descritta come la tecnologia che “permette alle persone e alle cose di essere connesse in qualsiasi momento, in qualsiasi luogo, con qualsiasi cosa e con chiunque, utilizzando idealmente qualsiasi percorso/rete e qualsiasi servizio”.
L’IoT è a sua volta abilitata grazie a diverse altre tecnologie.
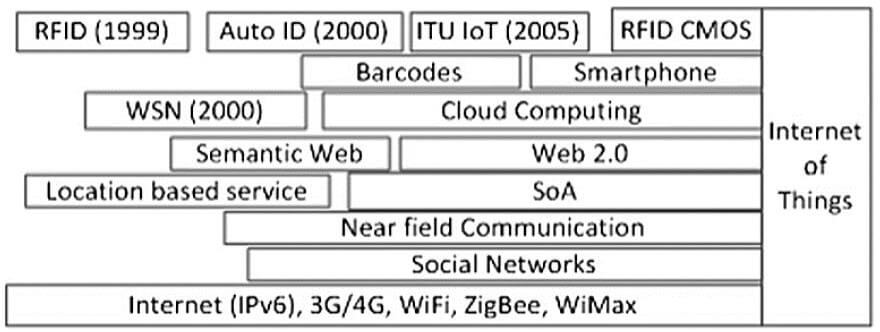
Figura 2 Tecnologie abilitanti per IoT
Per distinguere le applicazioni industriali con molteplici possibilità di impiego, viene spesso utilizzato il termine “Industrial Internet of Things” (IIoT), che è stato definito come “l’uso delle tecnologie dell’Internet of Things (IoT) nella produzione”.
Big Data and analytics
Grazie all’ampio utilizzo di sistemi di controllo distribuiti, nell’industria è stata raccolta una grande quantità di dati, i Big Data. L’interesse per le possibilità offerte dall’estrazione di informazioni da una così grande quantità di dati sta crescendo rapidamente. Il data mining, l’analisi e l’apprendimento delle macchine (AI, Machine Learning ecc.) sono tra le tecnologie considerate ogni giorno più importanti e fondamentali per sfruttare al meglio i Big Data.
Servono come strumento per migliorare la comprensione del processo, giocando un ruolo chiave nel contesto dell’industria. Infatti, i processi innovativi e progressivamente complessi richiedono sempre più l’uso di modellizzazione, monitoraggio, previsione e controllo dei processi basati sui dati. Lo scopo di queste tecniche è quello di esaminare i modelli dei dati di processo e le relazioni tra le variabili al fine di estrarre informazioni utili.
Simulazione
La simulazione è una tecnica che può essere utilizzata per prevedere il comportamento di sistemi complessi reali negli impianti industriali. In tal modo, la simulazione può fornire le conoscenze necessarie per supportare le decisioni di produzione, come la progettazione di layout di fabbrica, le interoperazioni della catena di fornitura, lo sviluppo di piani di produzione, la valutazione dei benefici e dei rischi delle strategie, l’ottimizzazione dei percorsi e l’assegnazione dei veicoli agli operatori, la pianificazione della capacità e l’ottimizzazione delle linee. Inoltre, l’uso della simulazione permette esperimenti per la validazione di prodotti, processi o progettazione e configurazione di sistemi, favorendo la riduzione dei costi, la diminuzione dei cicli di sviluppo e l’aumento della qualità del prodotto.
Cloud
Le piattaforme IT, basate sull’uso della tecnologia cloud, sono un supporto tecnico utilizzato dalle organizzazioni per la connessione e la comunicazione tra sistemi, sostenendo la crescente necessità di condividere e memorizzare i dati tra i siti e le aziende. Oltre alle abilità di storage il cloud potenzia anche quelle di elaborazione (cloud computing).
Il NIST, definisce il cloud computing come:
“un modello per consentire un accesso di rete on-demand ubiquo, conveniente e on- demand a un pool condiviso di risorse di calcolo configurabili (ad esempio, reti, server, storage, applicazioni e servizi) che possono essere rapidamente forniti e rilasciati con il minimo sforzo di gestione o di interazione con i fornitori di servizi”.
Descrive anche cinque caratteristiche che un modello di cloud ideale dovrebbe possedere: self- service on-demand, ampio accesso alla rete, pooling delle risorse, elasticità rapida e servizio misurato.
Sistemi integrati
Hanno l’obiettivo di rendere disponibili i dati per tutti gli attori rilevanti.
Il paradigma si estende in tre direzioni di integrazione:
- Integrazione orizzontale attraverso l’intera rete del valore: la connessione e il coordinamento di tutti gli attori della catena del valore ne permette l’ottimizzazione, creando un ecosistema molto dinamico;
- Integrazione end-to-end lungo l’intero ciclo di vita del prodotto: la capacità di immagazzinare ed elaborare le informazioni attraverso tutte le fasi del ciclo di vita del prodotto è essenziale per garantire la possibilità di miglioramento, non solo per quanto riguarda la produzione, ma anche per quanto riguarda la progettazione e i fornitori di materiali;
- Integrazione verticale e sistemi di produzione in rete: l’integrazione tra i diversi componenti e attori (come le risorse, le persone e i sistemi di esecuzione della produzione) permette di ottimizzare il processo.
Realtà aumentata
Realtà aumentata è un termine usato per descrivere una versione migliorata della realtà in cui la visione del mondo fisico (dal vivo o meno) è aumentata con immagini sovrapposte, generate da un computer. Questa tecnologia potrebbe essere utilizzata per migliorare sia il processo di progettazione che le operations.
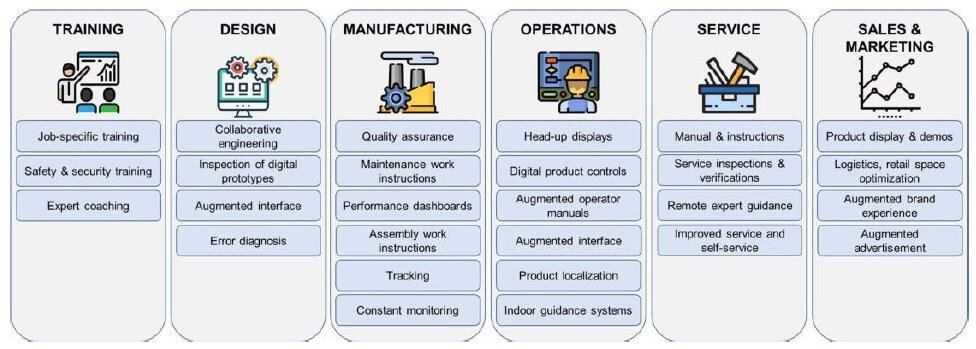
Figura 4 Applicazione della Realtà Aumentata nel contesto industriale.
La realtà virtuale invece, permette di costruire un mondo completamente virtuale con cui interagire. Queste tecnologie possono essere di grande aiuto al mondo industriale in quanto permettono di simulare rapidamente scenari che altrimenti richiederebbero tempo e investimenti.
La realtà virtuale e la realtà aumentata sono tecnologie preziose per semplificare le operations in quanto possono essere utilizzate per guidare gli operatori durante il loro lavoro. Inoltre, possono essere utilizzate come strumento per ridurre il time-to-market in fase di progettazione in quanto offrono la possibilità di impostare processi di produzione completamente simulati.
Robot autonomi
Oggi i sistemi robotici sono utilizzati in molte applicazioni, soprattutto per compiti altamente ripetitivi e/o eseguiti in ambienti e condizioni non adatte all’uomo. I robot stanno diventando sempre più autonomi, flessibili e cooperativi, iniziando ad interagire tra loro e con l’ambiente e a lavorare in sicurezza vicino agli esseri umani. Un robot autonomo è un robot flessibile che svolge i compiti assegnati in modo preciso supportando o sostituendo l’operatore.
Le nuove strategie nelle interazioni di interfaccia uomo-macchina stanno portando allo sviluppo di sistemi robotici collaborativi o sistemi “CoBot”, che permettono di sfruttare la forza e la resistenza dei robot con la flessibilità e il processo decisionale degli operatori umani.
Produzione additiva
Per soddisfare l’esigenza di una personalizzazione di massa, si stanno sviluppando nuovi metodi di produzione non tradizionali. La produzione additiva è in grado di soddisfare questa richiesta poiché può creare oggetti con attributi avanzati (nuovi materiali, forme complesse) e consentire una produzione delocalizzata, riducendo le distanze di trasporto e la necessità di magazzino.
Additive Manufacturing (AM) è un insieme di tecnologie che stampano modelli di prodotti CAD 3D. Originariamente la stampa 3D è stata utilizzata per sviluppare nuovi prototipi di prodotti (prototipazione rapida), poi è stata applicata nel Rapid Tooling, e ora mira a produrre prodotti finiti (Rapid Manufacturing).
Sicurezza informatica
Infine, la sicurezza informatica è una questione critica nel nuovo scenario industriale generato da questa rapida innovazione nell’archiviazione dei dati e nei dispositivi IT. Infatti, la crescente quantità di dispositivi collegati significa maggiori possibilità di attacchi informatici. Varie proprietà, come la riservatezza, l’integrità, l’autenticazione, l’autorizzazione, il non ripudio, la disponibilità e la privacy, devono essere garantite al fine di fornire sicurezza ai sistemi IoT.
Applicazione delle tecnologie 5.0 per la manutenzione predittiva
Al fine di fornire una panoramica delle opportunità derivanti dall’Industria 5.0 nel campo della gestione della manutenzione, i nove pilastri affrontati nella precedente sezione sono elencati di nuovo, facendo riferimento al loro possibile utilizzo nelle attività di manutenzione, nella Tabella 2.
Tabella 2 Panoramica dell’implementazione dell’Industria 5.0 nella gestione della manutenzione.
PILASTRO TECNOLOGICO | OPPORTUNITÀ DI APPLICAZIONE NELLA GESTIONE DELLA MANUTENZIONE |
Internet of things (IoT) | L’IoT consente la generazione di diversi tipi di strutture dati, che possono essere analizzate attraverso l’uso di tecniche di analisi avanzate (vedi Big Data Analytics) abilitando lo sviluppo di modelli previsionali di guasto. La connessione tra le macchine e la creazione di interfacce uomo-macchina promossa dall’IoT fornisce uno strumento per l’automazione delle contromisure di guasto. Infine, la presenza di dispositivi mobili può aiutare la supervisione delle operazioni manutentive, permettendo così ai manutentori di lavorare in modo più efficiente. |
Big data and analytics | I processi di manutenzione potrebbero trarre vantaggio dall’uso di modelli più complessi, come quelli di machine learning, nel tentativo di migliorare la politica di manutenzione e ridurre i tempi di fermo macchina. Infatti, a seconda della complessità dell’evoluzione del guasto, della disponibilità dei dati e della tecnica utilizzata, è possibile non solo rilevare i guasti negli asset ma anche operare un controllo diagnostico e/o prognostico, identificando la causa del guasto avvenuto ed anticipandolo. |
Simulazione | L’uso della simulazione può avvantaggiare i responsabili delle decisioni, sostenendo la scelta della giusta infrastruttura e delle politiche di manutenzione, fornendo informazioni sui costi-benefici delle potenziali alternative. Inoltre, la simulazione può essere utilizzata per prevedere il comportamento dei sistemi di produzione reali, supportando così le decisioni di pianificazione e manutenzione. |
Cloud | La presenza del cloud computing consente l’utilizzo di modelli più complessi (migliore capacità di memorizzazione ed elaborazione dei dati). La presenza di una piattaforma cloud può anche consentire l’archiviazione e la trasmissione in tempo reale di una massiccia quantità di dati potenziando le possibilità di apprendimento automatico dei modelli di previsione di guasto. |
Sistemi integrati | L’integrazione di tutti gli attori del sistema favorisce lo sviluppo di obiettivi di manutenzione con maggiore efficienza ed efficacia. Questa ampia integrazione di tutte le parti rilevanti nel business e nei processi a valore aggiunto e il collegamento della produzione e dei servizi di alta qualità attraverso tutta la catena del valore può garantire nuove opportunità, come l’implementazione di Smart Contract. In presenza di interfacce intelligenti, sarebbe possibile prevedere l’implementazione dello Smart Contract per gli interventi di manutenzione: una volta effettuato l’intervento, l’operatore manutentivo potrebbe interagire con la macchina che confermerebbe l’adempimento delle clausole del contratto, rilasciando automaticamente il pagamento. Inoltre, il servizio di manutenzione può essere effettuato anche da parti esterne (es. il costruttore) attraverso il monitoraggio continuo. |
Realtà aumentata | L’esecuzione di attività come gli interventi di set-up e manutenzione potrebbe essere notevolmente migliorata dall’utilizzo della realtà aumentata al fine di supportare gli operatori e migliorare la loro sicurezza, ad esempio, fornendo una guida da parte di un operatore più esperto attraverso una connessione remota o rendendo disponibili manuali tecnici. Inoltre, l’uso della realtà aumentata (o realtà virtuale) potrebbe fornire uno strumento più efficace per la formazione di nuovo personale, fornendo così la base di conoscenza necessaria per i compiti futuri. |
Robot autonomi | L’uso di robot potrebbe ottimizzare l’esecuzione di specifiche attività, aumentandone la velocità e la qualità. Inoltre, l’interazione uomo-robot può consentire un’esecuzione più sicura delle attività di manutenzione. |
Produzione additiva | La produzione additiva gioca un ruolo interessante nell’evoluzione della manutenzione, poiché la sua implementazione potrebbe consentire di creare pezzi di ricambio quando e dove sono necessari per ridurre i tempi di fermo macchina. |
Sicurezza informatica | La cyber-security è essenziale nella realtà industriale, indipendentemente dalle specifiche attività analizzate e la sua implementazione e miglioramento continuo è fondamentale per garantire la sicurezza di ogni membro dell’organizzazione. |
Conclusioni
Abbiamo descritto nel dettaglio le tecnologie promosse dal piano Industria 4.0 (ancora in corso) e dal nuovissimo Industria 5.0 e come queste possano essere fattori abilitanti anche per una nuova e innovativa gestione della manutenzione.
Come presentato nel precedente articolo, la manutenzione predittiva risulta ad oggi la nuova frontiera dell’innovazione per la gestione della manutenzione che si basa essenzialmente su 5 delle tecnologie abilitanti l’I5.0:
- Internet of things
- Big data and analytics
- Cloud
- Sistemi integrati
- Sicurezza informatica
Nel prossimo articolo scenderemo ancor più nel pratico presentando uno use-case nel mondo energy in cui è stato costruito un vero e proprio sistema di manutenzione predittiva.