Il concetto di gemello virtuale (o “digital twin” in inglese) è emerso all’inizio degli anni 2000, ma ha guadagnato una diffusione significativa solo negli ultimi dieci anni. Diverse ricerche stimano una crescita media annuale del mercato dei gemelli virtuali dell’ordine del 40%. L’esplosione di popolarità coincide con l’avvento e la diffusione di sensori intelligenti, dell’Internet delle Cose (IoT) e della disponibilità di enormi quantità di dati, che possono essere sfruttati anche in tempo reale, spesso attraverso algoritmi basati sull’intelligenza artificiale.
innovazione
Digital twin, come l’AI sta trasformando la produzione industriale
Il concetto di Digital Twin, nato nei primi anni 2000, ha guadagnato popolarità grazie a sensori intelligenti, IoT e big data. Utilizzato in vari settori, migliora progettazione e operazioni. L’AI crea modelli efficienti, riducendo costi e malfunzionamenti. Aziende di automotive, aerospazio e manufacturing ne traggono enormi benefici
Director AI-powered engineering & Digital Twin, Altair
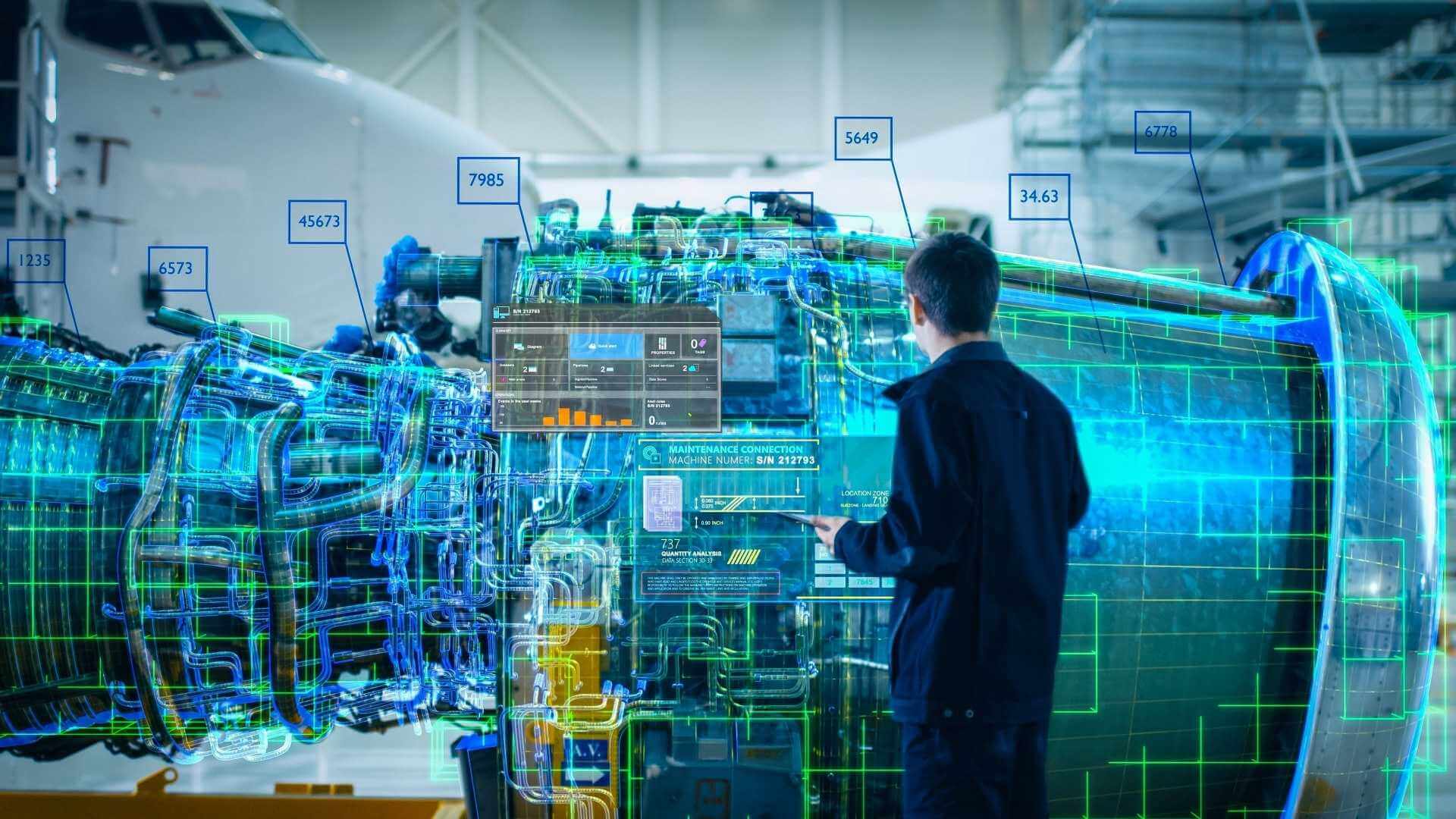
Continua a leggere questo articolo
Argomenti
Canali