«Tutto ciò che consente di modernizzare il processo produttivo ha sicuramente un impatto positivo in termini di back reshoring. Sappiamo che gran parte della delocalizzazione è avvenuta per risparmiare sui costi, quindi c’è stato un approccio iniziale per cui il costo era più importante di altri fattori, ora vediamo cambiamenti di percezione da parte del mercato, c’è maggiore attenzione alla qualità, e gli elementi relativi al miglioramento della qualità della produzione sono driver di Industry 4.0»: Luciano Fratocchi, Professore associato di Ingegneria economico gestionale all’Università degli studi dell’Aquila, nonchè co-fondatore dell’Uni-CLUB MoRe Reshoring Research Group, è positivo sull’opportunità che Industry 4.0 rappresenta come risposta alla delocalizzazione.
«Abbiamo già esperienze di back reshoring» aggiunge Giancarlo Capitani, presidente di Netconsulting Cube (consulenza IT), «per esempio in settori come il tessile e l’abbigliamento», che dopo una fase di delocalizzazione hanno riportato in patria le produzione effettuando «investimenti innovativi nella produzione, nella logistica» e valorizzando una filiera che parte dal design, dalla ricerca e sviluppo. Attenzione, però, non illudiamoci, commenta invece Carlo Alberto Carnevale Maffè, docente di Strategia e Politica Aziendale, Dipartimento di Management, Università Bocconi, «la delocalizzazione ha spostato il lavoro, e non è che con Industry 4.0 necessariamente torna il lavoro in Italia, il tasso di sostituzione robotica è più alto rispetto al reshoring». E’ vero che Industry 4.0 rappresenta un’occasione, perché «avvicinando domanda e offerta ha come effetto quello di riportare più vicino ai mercati di sbocco alcuni processi prduttivi», ma il rischio è che le produzioni si spostino in altri paesi europei, che stanno maggiormente puntando su Industry 4.0.
Posizioni diverse fra loro, dunque, che hanno dei punti in comune (industry 4.0 è un’occasione di recuperare punti per il manifatturiero italiano, e può senz’altro rappresentare un’occasione di back reshoring), ma che poi si allontanano quando si tratta di analizzare la situazione esistente e quello che l’Italia sta facendo per agganciare il treno della cosiddetta quarta rivoluzione industriale. La ricetta vincente, secondo Gianni Potti, presidente CNCT Confindustria Servizi Innnovativi e Tecnologici, è quella di «cogliere l’occasione di svecchiamento del sistema paese rappresentata da Industry 4.0 incrociando la manifattura classica e l’industria metalmeccanica con altri settori, ovvero i servizi innovativi e tecnologici, ripensando i processi produttivi e quindi la fabbrica».
Back reshoring: panorama internazionale
Partiamo dagli ultimissimi dati dell’Osservatorio dell’Uni-CLUB MoRe Reshoring Research Group, gruppo di ricerca che coinvolge le università di Catania, L’Aquila, Udine, Bologna, Modena e Reggio Emilia, che contiene i dati su 570 decisioni di revisione di precedenti strategie di off-shoring da parte di 459 aziende nel mondo, con alcuni di casi di decisione multipla. L’indagine evidenzia anche le differenti strategie scelte dalle aziende, in particolare differenziando le deciisoni di back reshoring (riportare in patria le produzione), da quelle di near reshoring (trasferimento di una produzione precedentemente delocalizzata in un paese più vicino rispetto a quello inizialmente scelto). In generale, emerge che il back reshoring si distribuisce in modo sostanzialmente omogeneo in Nord America (soprattutto negli USA), e in Europa, dove primeggiano i paesi a maggior tasso di industrializzazione fra cui l’Italia, insieme a Germania e Gran Bretagna. In generale, le imprese europee scelgono più frequentemente decisioni di reimpatrio multiplo. Le imprese italiane che hanno riportato in patria produzioni sono 86, con 114 decisioni (quindi, come si vede, in Italia prevale il rimpatrio multiplo). Ecco la situazione internazionale (aggiornata al giugno 2015).
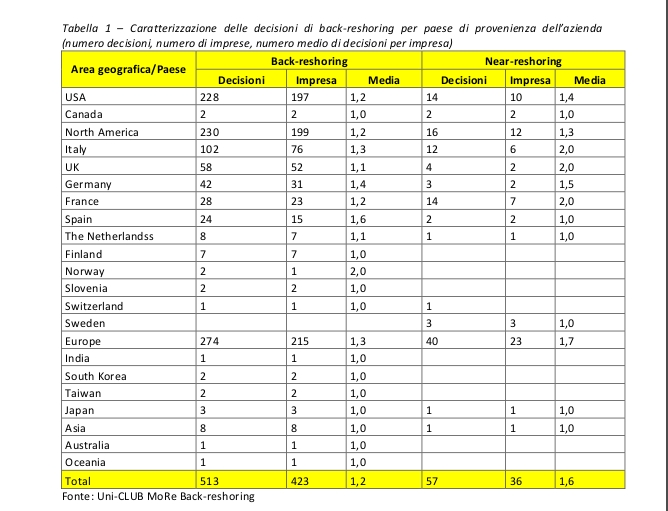
Il paese dal quale se ne vanno la maggioranza delle produzioni (80,8%) è la Cina (che era anche stata la destinazione più frequente per le operazioni di delocalizzazione). Attenzione: le imprese non abbandonano il paese asiatico, spesso riportano in patria singole parti del processo produttivo. Le decisioni di back reshoring dalla Cina sono 299, quelle di near reshoring 37. Seguono gli altri paesi asiatici (soprattutto il Sud Est asiatico), con 64 decisioni di back reshoring e 10 di near reshoring, e i paesi dell’Europa dell’Est, con 51 operazioni di back reshoring e tre di near reshoring. I rimpatri da Cina e Asia sono rilevanti sia verso l’Europa sia verso il Nord America, mentre quelle dall’Est Europa riguardano soprattutto il vecchio continente.
Il settore nel quale si verificano la maggioranza delle decisioni di back reshoring è quello delle attrezzature elettriche ed elettroniche (107 operazioni), seguito dall’abbigliamento (60), e dai macchinari industriali e computer (52). Nel near reshoring, invece, la parte del leone spetta all’abbigliamento, con 25 decisioni, mentre nessun altro settore raggiunge quota 10. Altri settori ad alto tasso di operazioni: attrezzature da trasporto (49), industrie manifatturiere varie (46), industria della pelle (43), strumenti di misurazione, analisi e controllo (30), manufatti in metallo, 27, gomma e plastica, 24, mobile e accessori per arredi, 22, alimentari, 14, chimiche, 12. Raggruppando i dati per settori estesi, il fashion sale a quota 104 operazioni (comprendendo anche accessori e occhiali), seguito da automotive, 64, elettrodomestici, 29, arredamento esteso (compreso tessile per arredamento), 25.
In generale, si evidenzia che il fenomeno riguarda tanto i comparti ad alto contenuto di innovazione tecnologica (come l’elettronico) quanto quelli più tradizionali (la moda), e si distribuisce sia nei settori ad alta intensità di capitale (automotive) sia in quelli ad alta intensità di manodopera (abbigliamento).
Rilocalizzazione in Italia
Come detto, le operazioni sono 113 (101 di back reshoring + 12 di near reshoring), implementate da 86 imprese. Si concentrano nei settori forti del Made in Italy, soprattutto la moda (45 operazioni, comprendendo anche accessori e occhiali), e a livello territoriale la parte del leone spetta al Veneto, e come macro area al Nord Est (35% delle operazioni). Perché le imprese italiane ritornano in patria? La motivazione più forte è l’effetto “Made in Italy”, ovvero il valore che il mercato riconosce al prodotto realizzato in Italia, (indicato per 37 operazioni di back reshoring e otto di near reshoring). Seguono:
- miglioramento servizio al cliente: 19 operazioni di back reshoring e cinque di near reshoring.
- Limitata qualità produzioni delocalizzate: 14.
- Crisi economica globale: 14 operazioni di back reshoring e quattro di near reshoring.
- Costi logistici: 11 rilocalizzazioni e cinque decisioni di near reshoring.
- Riorganizzazione aziendale: 11.
- Focus sull’innovazione (vicinanza ricerca e sviluppo e produzione): 10.
- Inadeguatezza maestranze locali: 8.
- Pressioni sociali nel paese d’origine (cioè l’Italia), ad esempio sul fronte sindacale: 8.
- Costi totali: sette operazioni di back reshoring e quattro di near reshoring.
- Riduzione del gap del costo del lavoro: sei operazioni di back reshoring e quattro di near reshoring.
- Disponibilità di capacità produttiva in Italia: 6.
Seguono altre motivazioni, fra cui elementi emotivi, scarsa attrattività del mercato locale, leggi sulla proproetà intellettuale. tempi di consegna, flessibilità organizzativa, incentivi governativi, dazi all’importazione. Come si vede, emerge il dato sottolineato da Fratocchi come elemento di particolare importanza in chiave Industry 4.0, ovvero il fatto che le motivazioni di carattere squisitamente economico appaiono relativamente trascurabili (a livello internazionale sono invece più rilevanti ad esempio negli USA). Questo è dovuto anche all’elevato costo del lavoro italiano (che non rende vantaggiosa in termini ecoomici la rilocalizzazione). A questo proposito, la ricerca definisce “meritevole di evidenziazione il fatto che gli esuberi di personale in patria e la disponibilità di capacità produttiva possono diventare una spinta alla rilocalizzazione, specialmente laddove le organizzazioni sindacali siano disponibili a rivedere gli accordi in termini di produttività per ora lavorata».
Si riconferma quindi, fra i fenomeni legati alle trasformazioni che Industry 4.0 è destinata a produrre nel mondo del lavoro, anche quella di un cambiamento nelle relazioni industriali.
Le analisi: pro e contro
La posizione più critica è quella di Carnevale Maffè, che parte dal seguente presupposto: la delocalizzazione è un fenomeno legato a costo del lavoro e produttività, Industry 4.0 invece è una «sostituzione dei processi produttivi di tipo tradizionale». Quindi, la delocalizzazione ha spostato il lavoro, e non ci sono evidenze che indicano che ora torni il lavoro. Si può parlare con maggior sicurezza di un “ritorno in Europa dei processi produttivi che prima erano andati in giro per il mondo”, e quindi di “near reshoring, ad esempio in Repubblica Ceca, Polonia”. Questo, perché la smart factory prevede un reengineering dei processi, che più che spostare la produzione, la cambiano e ne cambiano la natura. C’è una parte della forza lavoro che sarà ampiamente sostituito dalla robotica e dal software. Per lavori maggiormente qualificati, il discorso è diverso: “assumeremo più ingegneri? Non lo possiamo sapere, dipende. Non è mica detto che gli ingegneri di automazione industriale italiani siano i migliori. Cina e Corea formano personale qualificato, l’università italiana invece ne produce poco”. Fra l’altro, il villaggio è globale da tutti i punti di vista, quindi magari uno studente indiano viene a studiare ingegneria industriale in Italia e poi apre un laboratorio di ricerca industriale in America. In sintesi: “se non ci sarà un significativo cambiamento delle politiche didattiche, è improbabile che in Italia ci sia uno sviluppo sufficiente di professionalità per Industry 4.0. Al momento, non c’è sufficiente offerta di queste professionalità, non ci sono percorsi tecnici o universitari adeguati”, mentre ci sono paesi europei in cui invece esistono già professionalità per Industry 4.0, come la Germania. Certo, le singole aziende che esprimono eccellenze se la caveranno benissimo. Ma l’Italia deve lavorare di più su formazione e materia prima umana, su un forte coordinamento delle filiere. E poi, bisogna risolvere annosi problemi del fare impresa in Italia: governance, tasse, burocrazia, perché «se il paese è inefficiente, non cresce». Su Industry 4.0 «società e istituzioni devono essere coerenti, ci vuole un piano e una riforma profonda del paese che faccia funzionare meglio infrastrutture, trasporto, tecnologie infromatiche, scuola». Senza questa opera di coordinamento, si perde il treno.
Sulla necessità di un piano per Industry 4.0 è d’accordo anche Capitani: «il vero ostacolo è come fare Industry 4.0, coinvolgendo imprenditori e manager, che non sempre sono in grado di scegliere interventi da fare, investimenti, budget». Investire in innovazione e innovazione industriale non basta, «ci vuole una visione potente, una strategia, perché Industry 4.0 digitalizza tutte le fasi della produzione, della logistica, con strumenti nuovi». E’ una grande occasione anche sul fronte del reshoring, in particolare per settori chiave del Made in Italy, come il tessile, la moda, o ad alto tasso di innovazione, come l’ICT. Industry 4,0 «innovando fortemente tutta la catena (produzione, distribuzione, logistica), valorizzando ricerca e sviluppo, design, puntando su innovazioni con forte contenuto tecnologico, rende più conveniente riportare in patria la produzione». Non solo: la delocalizzazione ha in genere vantaggi in termini di costo ma anche svantaggi: barriere linguistiche, fusi orari, mentalità diverse. Su tutto questo, però bisogna puntare facendo un «piano di politica industriale, con obiettivi chiari per il paese, indicando quali strumenti e quali incentivi attivare».
Fratocchi, secondo il quale Industry 4.0 può senz’altro rappresentare una risposta alla delocalizzaizone, sottolinea l’importanza del fattore “Made in” emerso dall’indagine dell’Uni-CLUB MoRe Reshoring Research Group, che evidenzia “un intrinseco concetto di competenze posseduta dai lavoratori. Ad esempio, nel settore dell’abbigliamento l’importanza della competenza è fondamentale. Se a questo si uniscono processi di automazione, abbiamo una combinazione potentissima, perché l’automazione lavora su riduzione costi e ampliamento volumi, mentre la competenza dell’essere umano allevia complessità lavorazione, migliora le modalità di lavoro, alimenta innovazione di prodotto e di processo”. Analizzando i dati sul reshoring, si vede come in alcuni paesi, gli USA ma anche in Europa, il grado di automazione abbia aiutato la rilocalizzazione, quindi “mi sento di dire che Industry 4.0 possa supportare il fenomeno del reshoring, proprio perché interviene sull’area della produzione”. Due quindi i fattori fondamentali che collegano Industry 4.0 e rilocalizzazione: modernizzazione del processo produttivo, che consente anche di lavorare sui costi, e aumento del valore percepito dal cliente, attraverso la qualità del prodotto. Il docente, che come detto insegna ingegneria gestionale è più ottimista, rispetto a Carnevale Maffè, sulla formazione italiana in vista di Industry 4.0: «l’ingegnere italiano è riconosciuto nel mondo, senza dubbio, è un prodotto pregiato che esportiamo, se mi è consentito questo termine. Siamo riusciti a mantenere l’ampiezza di visione tipica dell’ingegnere italiano». E’ vero che Industry 4.0 richiede competenze trasversali, che spazino dall’ingeneria all’economia alla tecnologia. Ma «secondo me questo significa lavorare sulla sensibilizzazione per una cultura interdisciplinare, per cui l’ingegnere meccanico deve saper parlare con l’informatico. Le nuove tecnologie, dall’Internet of Things alla stampa 3D, richiedono di saper combinare le due cose. E’ questo il grosso sforzo che si sta facendo, e che bisogna continuare a fare, superando un po’ gli approcci classici delle barriere (meccanico, elettronico, informatico). Ci sono sedi in Italia con corsi di ingegneria meccatronica, quindi trasversali. Ma l’importante è lavorare anche su variabili più soft, le cosiddette soft skill, che prevedono capacità di comunicazione, problem solving. Quindi, non tutte le competenze in capo a un singolo specialista, ma la interfunzionalità».
Si tratta di un modello su cui convergono anche molti studi sul modo in cui è destinato a cambiare il mondo del lavoro con Industry 4.0. E l’importanza dell soft skill è un punto di sintesi anche con Carnevale Maffè. E proprio per sensibilizzare gli imprenditori alle sfide di industry 4.0 lavora Confindustria Servizi Innovativi, con workshop dedicati alla formazione e non solo. Potti annuncia che riprende il roadshow dedicato a Industria 4.0, che nel 2015 ha toccato Ancona, Napoli, Brescia, Roma, e che il prossimo 18 riparte da Parma. Fare cultura fra imprenditori, per cambiare le aziende, significa sviluppare il sistema produttivo italiano e anche creare le condizioni per riportare a casa aziende che avevano delocalizzato. Le risposte al lavoro fatto fino ad ora sono positive soprattutto da parte degli imprenditori metalmeccanici, anche grazie a iniziative con Federmeccanica. Fra le richieste degli imprenditori, quella di rendere più flessibili i bandi europei, unificandoli per i diversi settori, e di puntare maggiormente su forme innovative di aggregazione, come i contratti di rete.