Lo scenario competitivo in cui le aziende si trovano a operare è evoluto in modo molto rapido e profondo negli ultimi anni, rendendo la permanenza sul mercato una sfida sempre più impegnativa. In molti settori, queste evoluzioni hanno messo in crisi il paradigma produttivo della “Mass Production”, non più necessariamente idoneo a far fronte in modo efficacie e efficiente ad un differente profilo di domanda, tendenzialmente caratterizzato da:
· Diminuzione dei volumi: nonostante timidi segnali di ripresa, il mercato è ancora in una fase di stagnazione[1], con una domanda complessiva (in particolare nei mercati occidentali) in calo, solo parzialmente bilanciata da una crescita delle richieste da parte di (alcuni) paesi emergenti;
· Aumento della complessità: i prodotti richiesti devono sempre più spesso soddisfare requisiti più stringenti, anche in termini di servizi associati. In questo senso, la manifattura smetterà di essere semplicemente la produzione di beni materiali e si sposterà sempre di più verso l’offerta di soluzioni, in cui il prodotto fisico fungerà da abilitatore di un’ampia gamma di servizi immateriali;
· Aumento della personalizzazione: sempre più spesso il cliente richiede la personalizzazione del prodotto, per soddisfare esigenze di unicità; per stare sul mercato le aziende saranno “costrette” ad ampliare la gamma, cercando di produrre in modo efficiente (= con costi contenuti) minori quantità di un maggior numero di articoli. Trattasi della ben nota “coda lunga” di Chris Anderson[2], che già nel 2006 aveva intuito questo cambio di paradigma, oggi sotto gli occhi di tutti.
Per operare in un contesto più complesso ed in continua evoluzione, vengono ora richieste competenze e strumenti differenti rispetto al passato. Frammentazione dei mercati, ciclo di vita dei prodotti sempre più compresso, prestazioni richieste sempre più elevate e forte aumento delle personalizzazioni, sono solo alcune delle direttrici che spingono nella direzione della personalizzazione di massa, paradigma grazie al quale è teoricamente possibile produrre lotti molto piccoli (anche unitari!) a costi contenuti, rispettando target di servizio stringenti.
Un aiuto per far fronte a queste nuove sfide può arrivare dalle tecniche di Additive Manufacturing. È oramai consolidata l’idea che, in generale, queste tecniche siano economicamente valide per la produzione di lotti ridotti (poche decine/centinaia di pezzi) di oggetti piccoli e complessi[3]. Tuttavia, è molto raro che si identifichino soglie numeriche ben precise: quante unità devono comporre il lotto affinché risulti conveniente la stampa 3D rispetto alla manifattura tradizionale? Quanto deve essere complesso un componente perché le tecniche additive siano più efficaci rispetto a quelle per asportazione di materiale? Sono queste alcune delle domande che le aziende che approcciano le tecnologie additive (giustamente) si pongono, e a cui spesso non sono in grado di dare una risposta.
Per questa ragione, il Laboratorio RISE dell’Università di Brescia, ha messo a punto uno strumento in grado di supportare le imprese nel comprendere le potenziali applicazioni della tecnologia, valutandone la fattibilità tecnica ed economica e stimandone i benefici rispetto allo scenario corrente. Partendo dall’esplicitazione delle esigenze aziendali, si ottiene in output un’indicazione di quali tecnologie, macchinari e materiali potrebbero essere preferibilmente utilizzati, e a che costo.
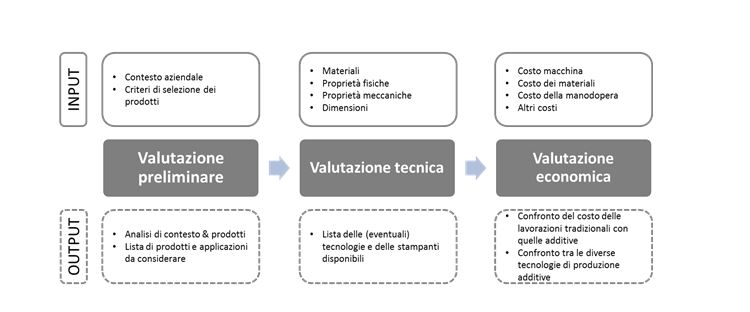
Figura 1- Percorso di analisi sviluppato dal laboratorio di ricerca RISE dell’Università degli Studi di Brescia
Il primo step prevede la valutazione del contesto aziendale, cioè dello scenario in cui opera l’azienda. Grazie a questa prima fase, i ricercatori sono in grado di guidare l’azienda nell’individuazione dei principali ambiti applicativi che ha senso considerare, rispetto a quelli che invece è bene escludere sin da subito in quanto palesemente non adeguati per l’applicazione della stampa 3D. Sebbene tale step possa apparire scontato, si segnala che spesso, al contrario, le aziende si scontrano con l’incapacità di svolgere questa valutazione, sottostimando i potenziali ambiti applicativi o, peggio, sovrastimandoli, ritenendo possibili applicazioni non ancora disponibili. In questa fase, si valutano quindi aspetti legati alla complessità dei prodotti, alla loro dimensione, al loro processo produttivo, ai materiali impiegati, mappando tutti questi elementi e circoscrivendo l’area dell’analisi. Riferendosi al quadro di valutazione proposto da Conner et al. nel 2014[4], sono 3 gli elementi basilari da considerare nella valutazione di quali prodotti (o famiglie di prodotti) possano sensatamente essere oggetto di valutazioni tecnico-economiche più approfondite: la complessità del prodotto, il livello di personalizzazione richiesto dai clienti ed i volumi generati.
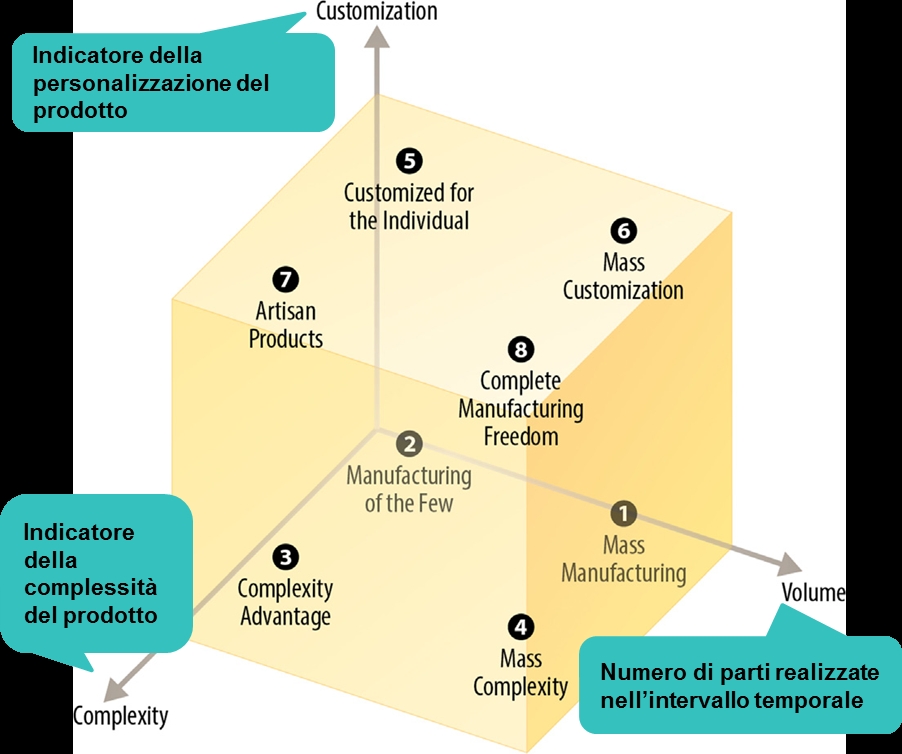
Figura 1– Elementi per la valutazione preliminare (adattato da Conner et al., 2014)
Al termine di tale valutazione preliminare, l’azienda diviene cioè consapevole del fatto che abbia senso (o meno) continuare a nutrire dell’interesse nei confronti di (quale) tecnologia, per fare cosa in quale area del proprio business.
In seguito, viene eseguita una valutazione di natura tecnica. Tale step è possibile grazie all’utilizzo di un database proprietario in cui sono state raccolte svariate informazioni inerenti le stampanti 3D professionali acquistabili in Italia. Ad oggi tale archivio consta di 110 stampanti, catalogate per: materiali stampabili, dimensioni stampabili, tolleranze dimensionali ottenibili, finitura superficiale, costo di acquisto e altre prestazioni di stampa. Grazie a questo strumento, è possibile incrociare le esigenze dell’azienda (in termini di caratteristiche fisiche e meccaniche dei prodotti) con le specifiche delle stampanti mappate, al fine di individuare il sotto-insieme di macchine/tecnologie che possano garantire il soddisfacimento dei requisiti tecnici. L’output di questa fase è quindi la lista di tecnologie, stampanti 3D, materiali e rivenditori, in grado di supportare l’azienda nella realizzazione di quei prodotti individuati nella valutazione di fattibilità preliminare.
Infine, viene sviluppata un’analisi economica, con l’obiettivo di valutare l’effettiva convenienza economica delle applicazioni di stampa 3D proposte allo step precedente. In questo senso, attenzione agli economics immediatamente valutabili, ma anche ai possibili benefici in esercizio dei prodotti così realizzati. Spesso, infatti, grazie alle tecniche additive, le aziende hanno la possibilità di progettare/realizzare prodotti con forme e geometrie avanzate, in grado di offrire prestazioni / funzionalità incrementate, tali da garantire il soddisfacimento di esigenze prima ritenute aldilà delle potenzialità delle tecnologie tradizionali. Il superamento di questi limiti spesso si traduce in un minore costo di gestione dei prodotti durante la loro vita utile. A titolo esemplificativo, si pensi agli iniettori di carburante per aeromobili, realizzati con tecnologie additive da General Electrics; sebbene il costo di produzione sia superiore rispetto al passato, il minor peso è in grado di generare risparmi di qualche ordine di grandezza superiore in termini di costi di esercizio, in primis in relazione al minor consumo di carburante.
Il modello realizzato permette di effettuare una costificazione delle applicazioni di stampa 3D (proposte dalla fase precedente di valutazione tecnica) e poi di comparare tali costi con quelli della manifattura tradizionale.
I costi delle applicazioni della stampa 3D sono ascrivibili a quattro categorie principali: macchina, materiali, risorse umane, attrezzature accessorie. Per ciascuna voce di costo è stata sviluppata un’opportuna metodologia di calcolo, che tiene conto delle caratteristiche specifiche delle diverse tecniche di stampa (tempi di produzione, tempi di intervento dell’operatore umano, coefficienti correttivi per la velocità di stampa, coefficienti per le strutture di supporto e per lo scarto di materiale, etc.).
Tale modello, applicato alle diverse stampanti 3D fornite in output dalla fase precedente, consente di selezionare la migliore soluzione possibile dal punto di vista economico. In Figura 3viene mostrato uno degli output del modello: considerando due differenti tecnologie (entrambe in grado di soddisfare i bisogni dell’azienda), a cui sono associate due specifiche stampanti, viene eseguito un confronto tra le varie voci di costo, in modo da poter valutare quale delle due stampanti sia da preferire.
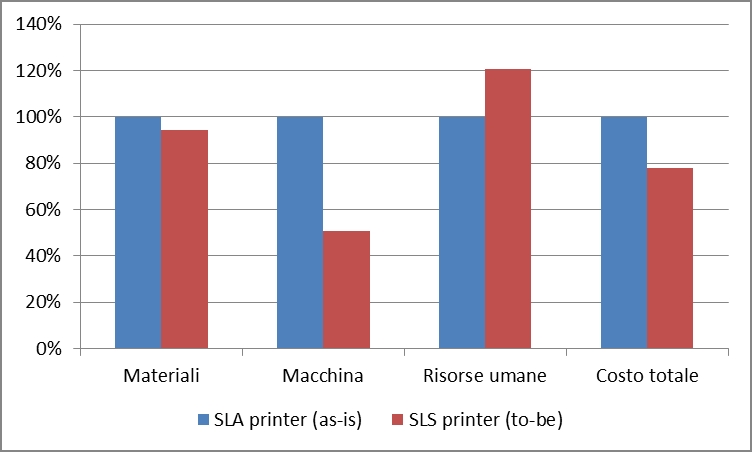
Figura 2– Esempio di confronto economico tra due tecnologie (stampanti)
Una volta selezionata la tecnica additiva preferibile, è possibile confrontarne i costi con quelli legati alle tecniche di manifattura tradizionali. Generalmente, se nella produzione con tecniche tradizionali sono utilizzati stampi o altre attrezzature dedicate, che quindi costituiscono un importante costo fisso, la stampa 3D risulterà conveniente per ridotti volumi produttivi, fino ad un certo break-even point, opportunamente calcolato (Figura 4).
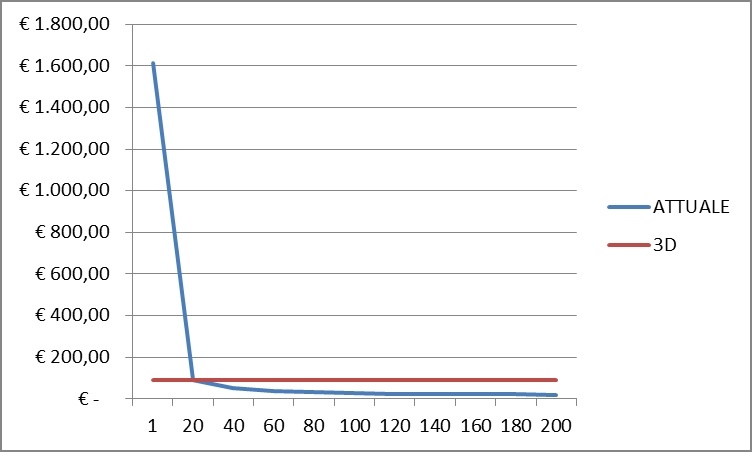
Figura 3– Esempio di confronto tra Stampa 3D e produzione tradizionale, con evidenziazione del break-even point
[1] Scenari economici n. 19 – La difficile ripresa. Cultura motore dello sviluppo – dicembre 2013 – Confindustria
[2] Chris Anderson, The Long Tail: Why the Future of Business is Selling Less of More, 2006
[3] Additive manufacturing paths to performance, innovation, and growth – Deloitte – 2014
[4] Conner et al. (2014). Making sense of 3-D printing: Creating a map of additive manufacturing products and services