Le aziende italiane (ma non solo) stanno affrontando un periodo storico ricco di cambiamenti che si susseguono a velocità notevolmente superiore rispetto a quanto già accaduto nel passato. La capacità di saper anticipare, o quantomeno cogliere con rapidità, le direttrici di questo cambiamento, è diventata un fattore competitivo chiave.
La globalizzazione e la rivoluzione digitale hanno radicalmente cambiato la sostenibilità del paradigma economico tradizionale: l’innovazione di prodotto oggi non è più sufficiente. Per rispondere a questi cambiamenti, occorre modificare la propria offerta, talvolta il proprio modello di business. Di fatto, occorre muoversi da una visione prodotto-centrica ad una orientata al concetto di “soluzione”, intesa come integrazione tra prodotto fisico e servizio immateriale. In questo senso, il servizio smette di essere il “male necessario”, e diventa il cuore dell’offerta. Tale strategia di servitizzazione, resa possibile (anche) grazie al supporto di potenti strumenti informativi, si manifesta in servizi efficaci ed efficienti lungo il ciclo di vita dei prodotti. In alcuni casi, anche in modelli di business innovativi, in cui ciò che viene venduto non è più il bene fisico, bensì il servizio ad esso associato (es. disponibilità della macchine, ore di volo di un motore, contratti pay-per-performance, etc.). In sintesi: l’attenzione non è più sull’acquisto del bene, bensì sull’uso della soluzione[1].
L’Internet delle Cose a supporto della servitizzazione
Una delle tecnologie in grado di abilitare questa “rivoluzione dei servizi” è sicuramente l’Internet of Things (d’ora in poi: IoT). Con l’IoT ogni oggetto è potenzialmente in grado di scambiare in modo autonomo informazioni con gli oggetti circostanti, modificando anche il proprio comportamento in funzione degli input ricevuti.
Secondo Gartner, l’IoT si trova oggi proprio sul picco delle aspettative dell’Hype Cycle (Figura 1): del resto, si tratta di un tema molto discusso, sebbene le applicazioni effettive siano ancora ridotte e i risultati richiedano ancora tempo prima di poter essere pienamente quantificati. Non a caso, Gartner stessa stima serviranno ancora 5-10 anni per arrivare alla maturazione definitiva, coerentemente con la necessità da parte dei provider di creare piattaforme, protocolli ed ecosistemi di sviluppo integrati su scala mondiale, in grado di garantire (anche) la sicurezza dell’interazione tra gli oggetti in real time. Le attuali applicazioni sono state infatti implementate in versioni create ad hoc, utilizzando diversi standard per lo sviluppo e il deployment.
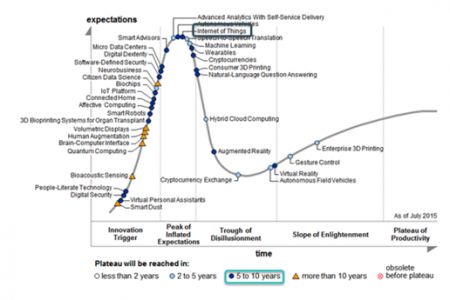
Dove sta il legame tra l’IoT e la servitizzazione di cui sopra? Ebbene, un elemento chiave della servitizzazione è costituito dal ritorno delle informazioni dai luoghi di utilizzo verso quelli di produzione. In altre parole, un’azienda è abilitata a modificare il proprio modello di business se e solo se è in grado di conoscere perfettamente lo stato di funzionamento del prodotto nello specifico contesto in cui è inserito; solo così potrà scientemente elaborare specifiche politiche di manutenzione legate all’effettivo “utilizzo” del prodotto (i.e. pay-per-use, pay-per-availability, pay-per-performance).
Il caso di successo per eccellenza in questo senso è rappresentato dal percorso della ben nota azienda britannica Rolls Royce, che sin dalla fine degli anni ’90 ha deciso di focalizzare sempre più l’attenzione non solo sul prodotto (motori per aeromobili), bensì sui servizi post-vendita ad esso associati. Nello specifico, la nuova strategia service-oriented si focalizza sulla possibilità di raccogliere dati in tempo reale sul funzionamento dei prodotti globalmente distribuiti: i dati, rilevati da sensori avanzati capaci di auto-diagnosi e controllo, vengono inviati in tempo reale al centro operativo dove sono elaborati, fino a generare report contenenti segnalazioni poi interpretate dagli ingegneri. La finalità è definire una politica pay-per-use in cui il cliente possa pagare solo le ore di funzionamento effettive del prodotto. Ebbene, ad oggi circa il 50% del fatturato aziendale deriva proprio dalle attività di service, in particolare dai contratti di manutenzione “Total Care” (della durata di 7-20 anni), che coprono quasi il 70% della flotta civile su cui si trovano le turbine R-R.
Storie di successo in Italia
Per citare un caso di successo nel nostro paese è possibile fare il nome della piacentina MCM, che realizza centri di lavoro di altissima precisione. Già da qualche tempo, l’azienda dispone di sistemi di raccolta dati avanzati, in grado di rilevare lo stato di avanzamento delle attività produttive della propria base installata. Grazie alla disponibilità in real time di queste informazioni sull’utilizzo delle macchine presso i clienti, MCM mette a disposizione degli stessi servizi di programmazione e pianificazione della produzione e di gestione predittiva delle attività di manutenzione. Il valore aggiunto del servizio è davvero molto elevato, visto che permette al cliente di focalizzarsi sulle proprie attività core, delegando al fornitore la gestione e la pianificazione delle attività produttive e manutentive.
Un altro caso interessante vede come protagonista uno dei più grandi produttori di caffè del Piemonte, il quale, implementando la tecnologia IoT nel suo ciclo produttivo, ha migliorato l’utilizzo della materia prima in tutte le fasi del ciclo produttivo, andando così ad eliminare significative quantità di scarti. Trattasi di una applicazione in grado di abilitare il controllo e la tracciatura dei flussi di prodotti e dati all’interno dell’azienda.
Un altro rilevante caso applicativo prende in considerazione un produttore di tubi senza saldatura. In questo caso, la tecnologia IoT (qui intesa come evoluzione della sua forma basica RFID) impatta sul processo di manutenzione delle attrezzature. Un’azienda di processo come quella in esame, richiede la massima operatività ed efficienza dei propri impianti, da cui deriva una riduzione/eliminazione dei tempi di fermo. Nel caso specifico, i dati raccolti permettono di monitorare e controllare lo stato delle attrezzature in ogni fase del ciclo di lavorazione. Concretamente, il responsabile della manutenzione, con l’ausilio di dispositivi tablet interconnessi con sistemi di lettura RFID, gestisce in real time lo “stato di salute” della linea, grazie alla tracciabilità completa delle informazioni di ogni item in corso di lavorazione. Conseguentemente, gli operativi di fabbrica hanno accesso alle stesse informazioni, potendo così preparare le attrezzature e le linee di laminazione più idonee al tipo di lavorazione che si andrà ad eseguire. I benefici sono evidenti: riduzione degli interventi straordinari durante i cicli produttivi e compressione dei tempi di setup.
Evidenze empiriche
Recentemente, una ricerca condotta dal Laboratorio RISE dell’Università di Brescia (The Digital Manufacturing Revolution), ha tracciato lo stato dell’arte riguardante la diffusione delle tecnologie digitali (tra cui l’IoT) nell’industria italiana. Dai risultati ottenuti (circa 100 aziende partecipanti), si evince come l’IoT non abbia ancora fatto pienamente presa nel mondo manifatturiero: più della metà del campione non conosce la tecnologia, e solo il 5% ne ha una piena consapevolezza (Figura 2).
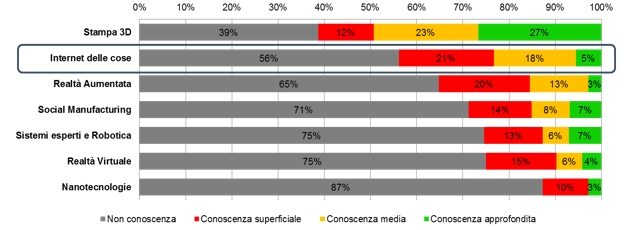
Sebbene quindi le potenziali applicazioni siano teoricamente chiare, nella pratica gli effettivi utilizzi sono ancora molto sporadici. Perché questo accade? In primis, le aziende denunciano gravi difficoltà nel reperire risorse umane competenti su questi temi, sia al proprio interno, sia all’esterno. In secondo luogo, come dimostrano alcuni studi della sezione Machinery della community ASAP SMF, una delle principali difficoltà nell’adozione di nuove offerte orientate al servizio, risiede nell’incapacità da parte del costruttore di gestire correttamente il rischio operativo e di sensibilizzare il cliente verso una nuova cultura del servizio.
In definitiva, è quindi fondamentale sensibilizzare sempre di più le aziende verso questi temi, spingendole ad acquisire consapevolezza prima e competenze poi; solo così potranno poi concretamente ed efficacemente inserire le nuove tecnologie digitali (in primis l’IoT) all’interno dei propri prodotti e processi.
[1] Brax, S. and Jonsson, K. (2009), “Developing integrated solution offerings for remote diagnostics”, International Journal of Operations & Production Management, Vol. 29 No. 5, pp. 539-60.